DIN Conversion Kit for Apeks (Chrome)
- Converts an Apeks XTX series Yoke (aka "A-Clamp") first stage to a native 300 Bar DIN fitting
- All metal handwheel with a polished chrome cosmetic finish
- Fits the DS4 (XTX40), DST (XTX50), FSR (XTX200), FSR† (Tungsten), FST† (XTX100), and TEK3 first stages
- † The cosmetic finish on those two discontinued first stages will not match the polished finish of the handwheel
- DIN assembly is marine grade chromed brass
DIN Conversion Kit for Apeks (Chrome)
Yoke fitting is removed using a ¾-inch box-end (aka ring-spanner) wrench; DIN conversion kit is assembled with no lubrication using a 6mm hex key (aka Allen wrench) and torqued to {18.4 ft-lbs | 25 Nm} as per 2023 Apeks Global Spare Parts Guide. Dive Gear Express recommends the Yoke to DIN conversion be performed by a technician trained to service Apeks products.
Constructed from marine grade chromed brass, this kit will convert an Apeks XTX series Yoke (aka "A-Clamp") first stage to standard 300 Bar DIN fitting. The two piece design DIN threaded handwheel and stem also includes o-rings and sintered filter cone, plus an Apeks branded DIN dust cap. The polished chrome finish of the all metal handwheel will match the current DS4, DST, FSR, and TEK3 first stage bodies, but will not cosmetically match the now discontinued FSR (Tungsten) and FST (XTX100) first stages. The DIN fittings on Apeks regulators use an uncommon 111 size o-ring (i.e. the smaller one) in the nose of the fitting to seal with the valve outlet, To temporarily switch back to yoke then use a DIN-to-Yoke spin-on adapter.
Yoke fitting is removed using a ¾-inch box-end (aka ring-spanner) wrench; DIN conversion kit is assembled with no lubrication using a 6mm hex key (aka Allen wrench) and torqued to {18.4 ft-lbs | 25 Nm} as per the Apeks Global Spare Parts Guide. Dive Gear Express recommends the Yoke to DIN conversion be performed by a technician trained to service Apeks products.
Brand | Apeks |
---|---|
SKU | APX-RA112112 |
Weight | 0.300000 |
Customer Reviews
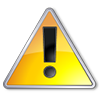
Availability of sub-assemblies and components, repair parts, specialized tools and maintenance manuals does not imply qualification to assemble and/or service scuba equipment.
Most authorized dealers are able to perform warranty, repair and service work on your equipment. Service by other than an authorized dealer may void the warranty. Improper service of dive equipment can lead to serious injury or death.
Dive Gear Express recommends that divers participating in more advanced technical and exploration type diving be trained in equipment service. We recommend that non-qualified individuals seek professional training/mentoring before attempting repairs or servicing on any diving equipment.
Uncoupling DIN Fittings From SCUBA Valves
There is more to disconnecting a DIN fitting from a valve than you might imagine. Do it incorrectly and you will probably lose an o-ring and perhaps even need to have your regulator serviced. The o-ring popping out of the nose of the DIN fitting is an issue on scuba regulators and fill whip hoses and it is caused by failing to completely bleed residual pressure before uncoupling the fitting.
When divers are unscrewing DIN fittings on first stages they may encounter the issue when hoses are longer than typical sport lengths or especially with oxygen compatible designs like our DGX Xtra and D6 that include flow restrictions for high-pressure gas. Briefly purging the second stage just once is not enough, residual pressure trapped in the high-pressure hose of the SPG will take several seconds to move all the way back through the regulator first stage to the second stage. You must wait a moment between each time you push the purge and you must do it three times in a row to fully release all the pressure from the hoses. Another equally effective two-handed technique is to continue to hold the second stage purge down in one hand while you begin to unscrew the DIN fitting using the other hand.
On fill whips, you can be certain all the pressure is released by opening the bleed and waiting a few extra seconds before starting to unscrew the fitting. You need to wait a moment after the hiss stops, because the bleed hole is tiny and gas will continue to escape even after the hissing stops. Compact ring-style bleeds found on fill whips that twist either direction to bleed are popular because you can't lose the bleed screw, but with this design you must make sure the ring is centered on the bleed opening because if you keep twisting you will close it again with out fully bleeding the hose.
DIN fitting designs use a two or three part assembly in which the threaded component with a handwheel collar slides onto a hollow center post and is retained by a 'nose cap' that contains the sealing DIN o-ring on the front and a smaller o-ring on the back. Improperly unscrewing the collared threads by rocking the entire assembly back and forth, or just using brute force to 'break' the seal can eventually can loosen the center post and/or nose cap causing a leak or seal failure the next time you try to use the fitting. We've seen the loosened nose cap act as a 'locking' mechanism, resulting in the fitting becoming frozen in to the DIN outlet and impossible to remove. Conversely, the "loose" nose cap can allow the 1st stage to "rotate" about the DIN fitting even when seemingly fully seated and pressurized. Sometimes you can 'save-a-dive' by using a hex wrench to hand tighten the DIN assembly but a loose assembly is nearly impossible to permanently correct in the field and usually requires bench service at the local dive shop to be able to fully tighten and lock the assembly back in place.
Proper technique to uncouple a DIN fitting requires you be careful to only turn the collar in the DIN fitting, don't grab and turn the entire assembly. If you can't easily turn just the collar to unscrew, i.e. you have to use force on the the entire assembly to 'break' the seal, then the line is not fully depressurized and you need to repeat the bleed.